|
|
|
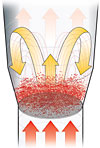
|
Very effective type of solid drying.
Outstanding heat transfer.
Unmatched speed of drying.
Gentle product handling.
Intensive mixing of the solid material.
Uniform, reproducible product quality.
|
|
|
Process advantages
Fluid bed drying represents a very effective type of solid drying (-> Drying). The whole surface of each individual
particle is available for drying in the flight phase. The heat transfer is
excellent and the drying time is ideal. The product is dried gently due to these
factors. A homogeneous product temperature and a uniform drying of the starting
product are achieved as a result of the continuous and thorough mixing. This
cannot always be guaranteed in the case of contact and radiation dryers. In
these cases, local hotspots are quite possible. If only a small amount of
water is to be evaporated, wet granules can also be dried directly in the Vertical Granulator: Single pot
process (-> Wet Granulation in the
vertical granulator).
|
|
Principles of operation
For the drying of granules, agglomerates and pellets, Glatt offers systems
with different capacities according to the process requirements, starting
materials and the desired product parameters: Continuous Fluid Bed Systems with
throughputs from 20kg to 5t/h. Batch Fluid Bed Systems with batch sizes
from 2g to 1.5t/batch.
Batch fluid bed
The moist starting product is fed batch-by-batch into the material container
of the dryer for drying. Here it is mixed vigorously in the upwards-pointing
heated gas stream and held in suspension. In doing so, it dries to the required
end moisture content with high heat and material transition coefficients. The
optimum gas speed depends essentially on the particle size and density. Heat is
fed in via the process air. The temperature of the air can be varied during the
drying process. After drying, the product can be cooled before the material
container is emptied and the next batch starts.
|
|
Principle: Batch fluid bed drying |
|
Continuous fluid bed
The activities that are carried out batch-by-batch in the above process, i.e.
at different times, are carried out in different places in the continuous
process. Moist starting product is fed in continuously and moves through the
process chamber. Effective drying is guaranteed by different temperatures of
the incoming air. If the last air chamber is operated with cold air, the dry
product can be cooled before leaving the process chamber.
|
|
Principle: Fluid bed drying in the continuous Glatt fluid bed (GF)
|
Principle: Fluid bed drying in the continuous Glatt fluid bed (GF)
Cooling in the last process chamber |
|
|
Reproducible process
No matter which system is used – the process must be reproducible. Premature
drying of the top layers of the granulate must be avoided at all costs. The
effects of the weather on the drying process must be eliminated. Glatt offers
fully-developed process technology and the facility to test and optimise drying
processes in the Glatt laboratory (-> Process Development).
Solvent drying
For the use of organic solvents, Glatt offers circulating gas systems with
proven safety for fluid bed processes and vacuum systems for fluid bed systems
and vertical granulators. (-> Solvent
Recovery) |